- Elisha Kasinskas
- |
- August 13, 2012
Empowered In-plants: Tell-All Success Stories from the Field– Session Panelist Close Up
This article is the third of a four part in-depth series introducing each of the successful in-plant panelists at the headliner event for the new in-plant education track at GRAPH EXPO. Titled "Empowered In-plants: Tell-All Success Stories from the Field," Rochester Software Associates (RSA) announced the session panelists chosen on July 19th
Debbie Gallagher, State of Oregon Government Secret: Integrate Print and Mail
Panelist Debbie Gallagher, Senior Operations Analyst, for the State of Oregon Department of Administrative Services (DAS) Publishing & Distribution (P&D) program, knows a thing or two about in-plant success. In fact, last year DAS Publishing & Distribution was named the fourth largest government in-plant (according to sales) by In-Plant Graphics magazine.
Publishing & Distribution (P&D) is the state's centralized provider for printing mailing and delivery services. Early in her tenure, Debbie focused on integrating state print and mail operations, leading the development of print-to-post (variable data print) processes at P&D and extended one-stop printing, mailing and delivery services to cities and counties. Later, she was a major contributor in consolidating Oregon state agencies' mailing operations, copy centers, and data center printing. As a proponent of automation and technology in the industry she led two multi-million dollar digital equipment replacement projects for this government in-plant.
When I first spoke with Debbie, without hesitation, she felt that the integration of print and mail was critical to this government in-plant's success.
Millions Budgeted and Served at this High Volume Government In-Plant
And the fruits of their labor have paid off in better utilization and lower costs for their 1,500 + customers located throughout the state.
"We are not Kinko's," states Gallagher. "We provide so much more than just printing." In fact, P&D offers a full range of services, such as graphic design, CD publishing, consultation and job planning, distribution and mailing, variable data printing and more. About half of what they print is variable, such as jury summons, and they also produce negotiable documents like titles, checks, and warrants. This government print center is truly a "one-stop-solution" to document design, print, process, and mail.
P&D has 86 employees in three locations, operating with a $15 million annual budget. An impressive 60% of their jobs enter the mail stream – 2.3 million pieces of mail are sent out monthly— at reduced postage rates. They have integrated a secure online package tracking system, with the state shuttle system. With their 12 delivery vehicles, they deliver to 550 stops daily up and down the I-5 corridor from Portland to Eugene.
Like many in-plants and government operations, they are not immune to reduced budgets. But, they meet them with aplomb and a confidence that their automation and heavy use of technology will help them continue to operate as efficiently as possible and allow them to continue to offer new services to customers.
Equipment and Software Are Continually Updated to Meet Customer Needs
Equipment at the in-plant includes an impressive array of Kodak and Ricoh printers, as well as stitchers, a perfect binder, a collator, folders, Guillotine cutters, shrink wrappers, and tape binders. On the mailing side, four Pitney Bowes smart mail inserters, cameras, a Pitney MLOCR mail pre-sorter, a high-speed ink-jet addresser, meters, and a strapper give P&D the muscle to meet customer needs in a single location continuous print and mail workflow. Software at the State of Oregon's in-plant make possible electronic print job ordering and tracking, variable data printing, address cleansing and updates, document editing, pre-flighting, scanning, and imposition; and data-stream transformation, output management, job conversion, address forwarding on the fly, end-to-end piece tracking and secure package tracking.
One Final Secret. Convenience and Customer Commitment Sustain the Operation
According to Gallagher, "We are fortunate to have employees and managers who are committed to the organization. We continue to look for the best solutions to meet our customers' needs. We refresh our equipment regularly to use technology to streamline job processes.… Convenience and a commitment to our customers go a long way in sustaining our operation."
Learn how these top in-plants in insurance, higher education, government and healthcare are building their success. Other panelists include: Jimmy Friend, University of North Texas (UNT) Director of Printing and Distribution Solutions, (PDS), Phil Larson, former Director of AFPress and grafaccent at American Fidelity, now President of Shepherd Consulting OK, and Gene Voelker, Manager Supply Chain Business Services, Parkview Health.
The panel will be moderated by Elisha Kasinskas, Marketing Director of Rochester Software Associates, developers of the top in-plant web-to-print software, WebCRD.
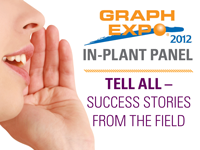
See the Full Session here
Watch and learn how 4 top in-plants make their print centers successful as they provide their insights at our Graph Expo 2012 panel session