- Howie Fenton
- |
- November 16, 2020
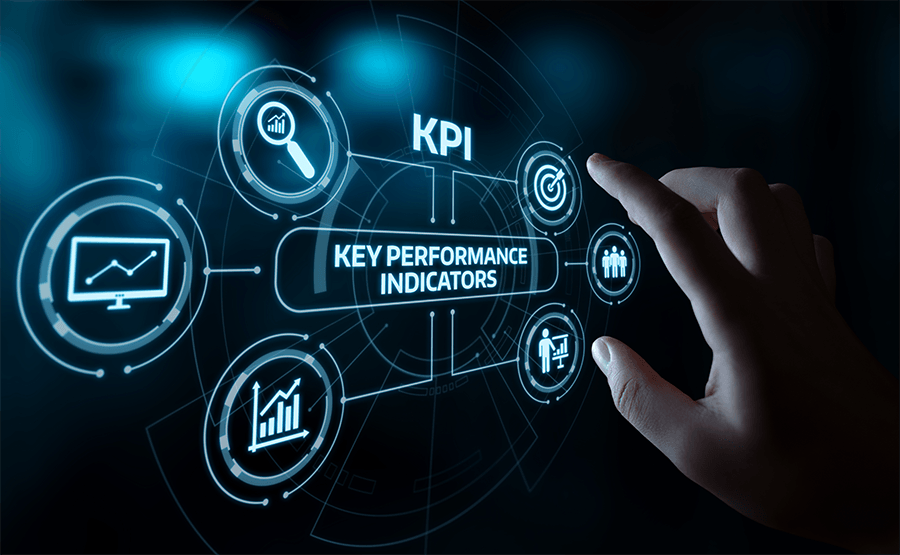
Measuring performance and analyzing how to improve productivity is perhaps the most important tool in your toolkit to prove your value as an in-plant print center. In addition, it will provide the information you need to keep prices competitive and the outsourcing wolves at bay. This is the second article in a two-part series that discusses issues with metrics. Part one of this series discussed the issue of bad metrics. In this article we discuss the four problems associated with manual data collection: unreliable data, staff productivity loss and dissatisfaction, and the inability to compile and analyze manually collected data. I believe this is the worst problem with data because almost half of in-plants collect data manually and most of those collect ALL their data manually.
Four Problems with Manually Collecting Data for Metrics
Manually collected data is information that is collected manually typically with pen and paper. Manual data collection is frequently an acceptable standard operating procedure when you are collecting a new measure. However, once you can know that a metric is worth collecting you need to automate the collection process and store the data to compile and assess. There are four common problems with continued use of manual data collection.
1. Good Manual Metrics Become Bad Batched Metrics
To fully understand the problems with manual data collection you must watch staff collect data over time. Based on my experience if you leave the data collection as a manual process, people tend to no longer write down the results after each occurrence and start to write it down in batches. This is a gradual process first every other time, then every fourth time and soon it is before lunch and before leaving. This can lead to once a day or even once a week recording. Each time the data recording is done in longer and longer batches the data becomes less and less reliable.
2. Manual Collection Slows Productivity
Each time someone must write something down, they reduce their productivity. It may only require 15 seconds to manually record a task, but if that occurs every minute, they are losing 25% of their time. That could result in 1.5 hours/day in lost productivity. This was the main complaint in the first attempt to automate data collection. Each work area had a keypad that required staff to input a staff number, task number, time number and material number. Often it took longer to input all the data than it did to perform the job, which lead to low compliance with the system.
Manual data collection also interferes with staff's ability to concentrate and get into a rhythm sometimes referred to as the "productivity zone". Staff that get into this zone report that it is the most productive time of their day. Collecting data manually record can disrupt this rhythm.
3. Staff Will Hate the Process
At first manual data collection is interesting to staff because it helps them better understand their process and may even lead to changes to increase their performance. In fact, one of the easiest ways to improve performance is simply create a chart with different lines representing different staff performance over the course of a week or month. Even without identifying the staff names on the chart, everyone will know their own performance and want to improve.
Over time however, staff will grow to resent the data collection and it could result in questioning the value of these measures. In some cases, the dissatisfaction can result in reporting sabotage. Some people will change the numbers and report inconsistent data hoping that it will stop the data collection.
4. Tough to "slice and dice" (analyze parts of) the data
Manual data collection is also harder to interpret because the data is not compiled and more difficult to interpret. It is hard to figure out trends or root causes. For example, some problems are related to time. They may only occur in the morning or on certain days. If this sounds familiar you may have heard of this before because it was described in the 1971 book Wheels. The books by Arthur Hailey claimed that cars built on Monday or Friday suffered from quality problems presumably due to late nights, hangovers, cutting corners and absenteeism.
But some printing and mailing facilities suffer from Monday problems, too. In some the digital presses and inserting equipment jam more often on Mondays than other days. Without compiling the data, you would never see this problem and identify the root cause which is usually associated with temperature and humidity. The point is that to make data useful for interpretation it should be gathered, compiled and then sliced and diced for the analysis.
Conclusion
As we discussed in part one of the series, just because you can measure something does not mean you should measure it, because not all measures help you monitor or improve performance. You should critically evaluate your metrics and analysis to determine if they are helping or hurting your facility.
Manual data collection is almost inevitable when you are first testing to determine if a metric is worth collecting, because in essence it is a proof of concept. Once you prove the value you need to automate the data collection, compile the data and start to analyze it.
Once you have proved the value of collecting that data you have to work to automate the process. Automating data collection is not easy. In some cases, you may take two steps forward and one step back in your attempt to automate, but that is natural.
Since the automation includes the collection, recording, and storing of data it is almost inevitable that you will need software. One of the best resources for automating data collection are your vendors. Talk to your Web to print, Print MIS and workflow software vendors like RSA about what they can offer. They will likely have solutions and possible integration strategies to help you automate your data collection.
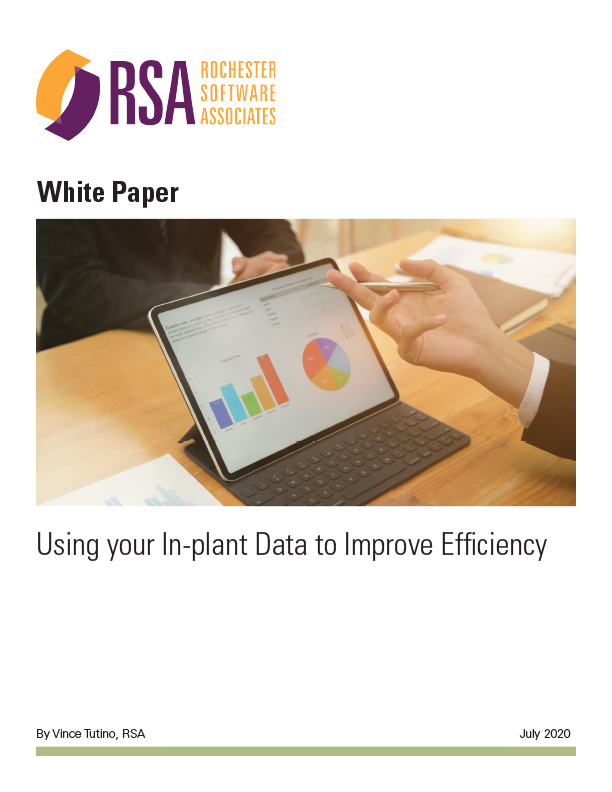
Download RSA's Newest Whitepaper
RSA has a nice white paper called, "Using Your In-plant Data to Improve Efficiency" that discusses automating data collection and how to use the data to improve your print shop.