- Howie Fenton
- |
- September 10, 2024
Key performance indicators (KPIs) are crucial yet challenging metrics to define and measure within the printing industry. Over the years, the graphic arts sector has struggled with consistent measurements, reporting, and process improvement strategies. This difficulty can be attributed partly to the lack of adequate tools and partly to a culture that often regards print production as more of an art than a science. In this blog, we'll delve into the importance of measurements and KPIs, strategies to gather the data, and offer insights into how they can be used effectively to enhance performance.
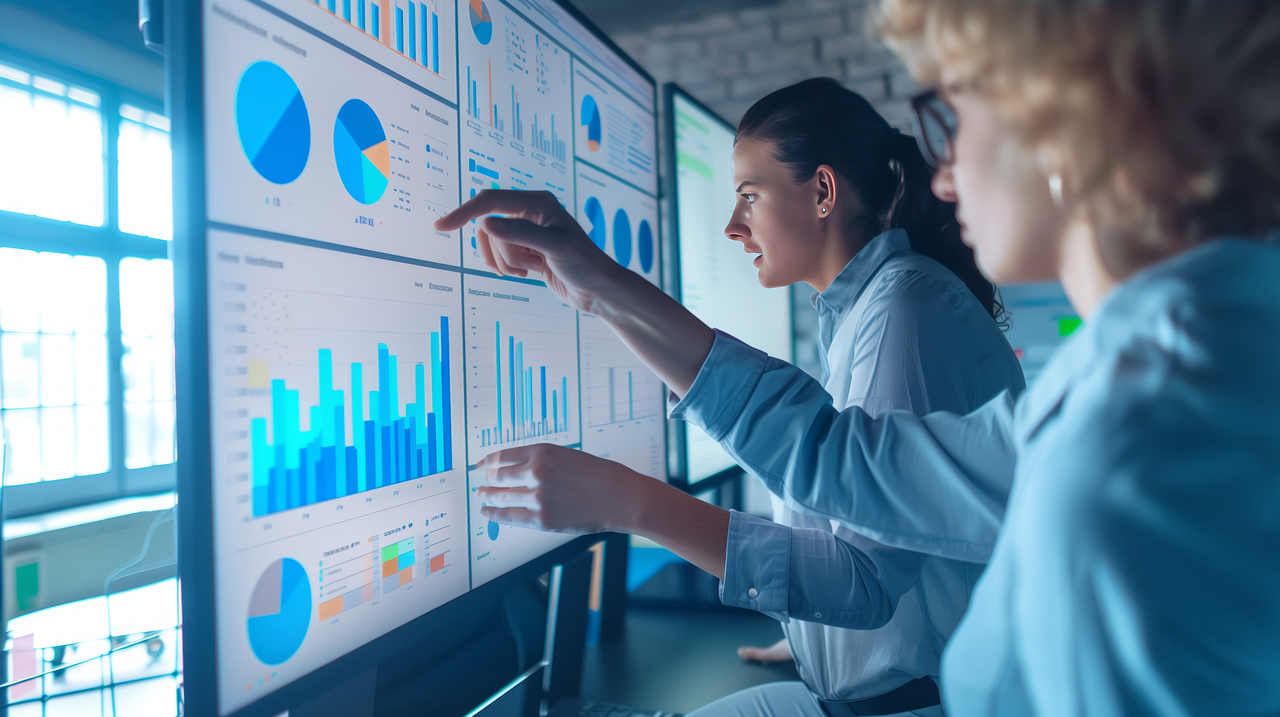
Insights from the NAPCO In-Plant Printing KPI Report
Recently, NAPCO Research published a comprehensive study titled the "In-Plant Printing KPI Report." This report sheds light on both the successes and challenges faced by in-plant printers. The study surveyed 134 in-plant printing facilities, with the largest categories being colleges and universities (32%), healthcare companies (15%), and school districts (14%). Operating budgets ranged from under $500,000 to over $4 million, with the majority (60%) of these facilities employing fewer than nine staff members, while 21% had 10 or more employees.
One finding is that over 86% of in-plants outsource a portion of their work, with the average amount of outsourcing being around 10%. More notably, 58% of in-plants are offering their services to external companies on insourcing. The percentage of revenue generated from these external sources varies widely, from 10% to over 50%, with an average of 17%. Interestingly, 61% of respondents indicated that the volume of outside work they handle is holding steady.
The Good and the Bad News: A Balanced Perspective
The Good News:
- Budget and Page Volume Growth: Budgets are on the rise, as are page volumes. This indicates that in-plants are securing more work and that their services are in demand.
- Increased Insourcing: The trend of insourcing, where in-plants offer services to external clients, is growing. This not only boosts revenue but also enhances the in-plant's strategic value to its parent organization.
- Low Outsourcing Levels: The relatively low percentage of outsourced work suggests that in-plants are capable of handling the majority of their print jobs internally, which could be a sign of strong in-house capabilities.
The Bad News:
- Low Utilization Rates: Many in-plants are not fully utilizing their equipment and staff, which can lead to inefficiencies and increased costs.
- High Rework Percentages: A significant amount of rework due to errors suggests that there may be quality control issues that need to be addressed.
- Questionable ROI: The return on investment (ROI) for in-plant printing facilities may be less than optimal, especially when considering the costs associated with underutilization and rework.
- Labor Challenges: The industry faces ongoing challenges in attracting and retaining skilled labor, which could impact the quality and efficiency of in-plant operations.
A Consultant's Approach to Measurements and KPIs
This year, I've had the opportunity to present on the topic of measurements and KPIs at major industry events such as IPMA (In-Plant Printing and Mailing Association) and Printing United. During these presentations, I introduced a report card system that I use to evaluate performance after completing a consulting assignment. This report card categorizes performance into World-Class, Industry Average, and Laggard (below industry average).
The metrics I assess come from a wide range of sources. Some are based on production volumes from various devices, including black and white printers, color printers, large format devices, and offset presses, and they are based on rolling averages I have analyzed in other in-plants. Others are derived from focus groups and surveys that measure key aspects like quality, turnaround time, pricing, and customer experience. Additionally, I evaluate the use of automation tools, such as Web-to-Print software, estimating software, and prepress PDF workflow systems. I also assess critical business functions, such as soliciting work, competitive pricing, and achieving financial goals. Lastly, I look at value-added services like managing large format printing, fleet management, mail services, fulfillment, and insourcing. Below is an example of what a typical report card I create in audits that indicates how I rate their performance benchmarked against leaders, industry average and laggards which are below average:
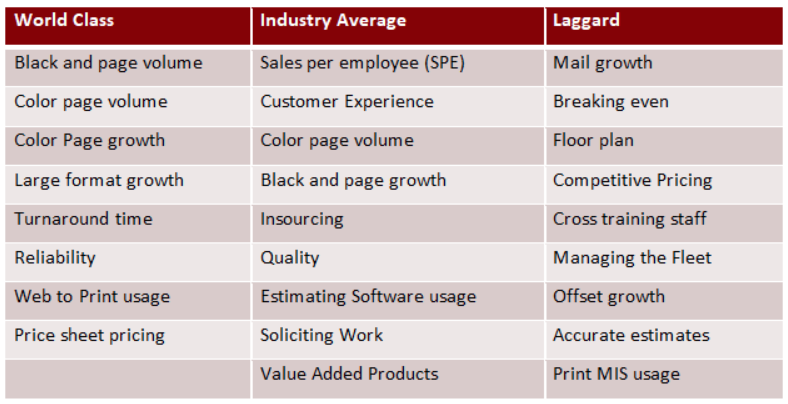
When examining the "World-Class" column, one of the first things that stands out is the emphasis on volume and growth. Volume refers to the page count or square footage (for large format), while growth reflects consistent increases in these volumes year after year. Metrics like turnaround time, reliability, quality, and customer experience are critical and are often measured using the Net Promoter Score (NPS) methodology to gauge satisfaction and loyalty.
This table is a fairly typical snapshot of how most evaluations look—not necessarily the specific metrics in each column, but due to the overall balanced distribution between World-Class, Industry Average, and Laggard categories. After reviewing this, many organizations realize they have a mix of strengths and areas for improvement. It’s common for leaders to express surprise, saying, "I thought we would be more World-Class and Industry Average, but I can see now that we have more work to do to achieve that status."
This realization is the first step toward targeted improvement, helping organizations focus their efforts where it will have the most impact on elevating their overall performance.
Moving Forward: Strategies for Improvement
To address these challenges and capitalize on the opportunities highlighted in both these reports, in-plant facilities should consider the following strategies:
- Enhance Efficiency: By improving workflow automation and investing in staff training, in-plants can reduce rework and increase utilization rates.
- Focus on Quality Control: Implementing more rigorous quality assurance processes can help reduce the need for rework, thereby improving overall efficiency and ROI.
- Leverage External Work: Continuing to grow the volume of external work can diversify revenue streams and increase the in-plant’s value to the parent organization.
- Invest in Technology: Upgrading equipment and adopting new technologies, such as AI and advanced automation tools, can help in-plants stay competitive and improve their service offerings.
- Implement Continuous KPI Reporting: If not already in place, invest in processes to automatically report on KPI data so that the effectiveness of changes made can be shown without manual efforts each over time (month, quarter, year, etc.). Print MIS systems and Web to Print systems, like WebCRD, often have the data needed to produce these KPIs, that can be joined with other corporate data to graphically show progress in each of the KPI areas.
In conclusion, while the in-plant printing industry faces several challenges, there are also significant opportunities for growth and improvement. By focusing on key performance indicators and strategically addressing areas of weakness, in-plants can enhance their value proposition and secure their place as vital components of their parent organizations.
Printing Measurements and KPIs: A Path to Performance Improvement
Key performance indicators (KPIs) are crucial yet challenging metrics to define and measure within the printing industry. Over the years, the graphic arts sector has struggled with consistent measurements, reporting, and process improvement strategies. In this blog, we'll delve into the importance of measurements and KPIs, strategies to gather the data, and offer insights into how they can be used effectively to enhance performance.