- Howie Fenton
- |
- August 06, 2024
In the printing industry, measuring productivity, reporting on performance, and identifying and overcoming production issues are all crucial tactics when it comes to remaining competitive.
Getting these right means looking at various metrics that show how efficiently your production processes work. Reporting is about gathering and analyzing all of this information, then presenting it to the right people to help them make better decisions and facilitate improvements.
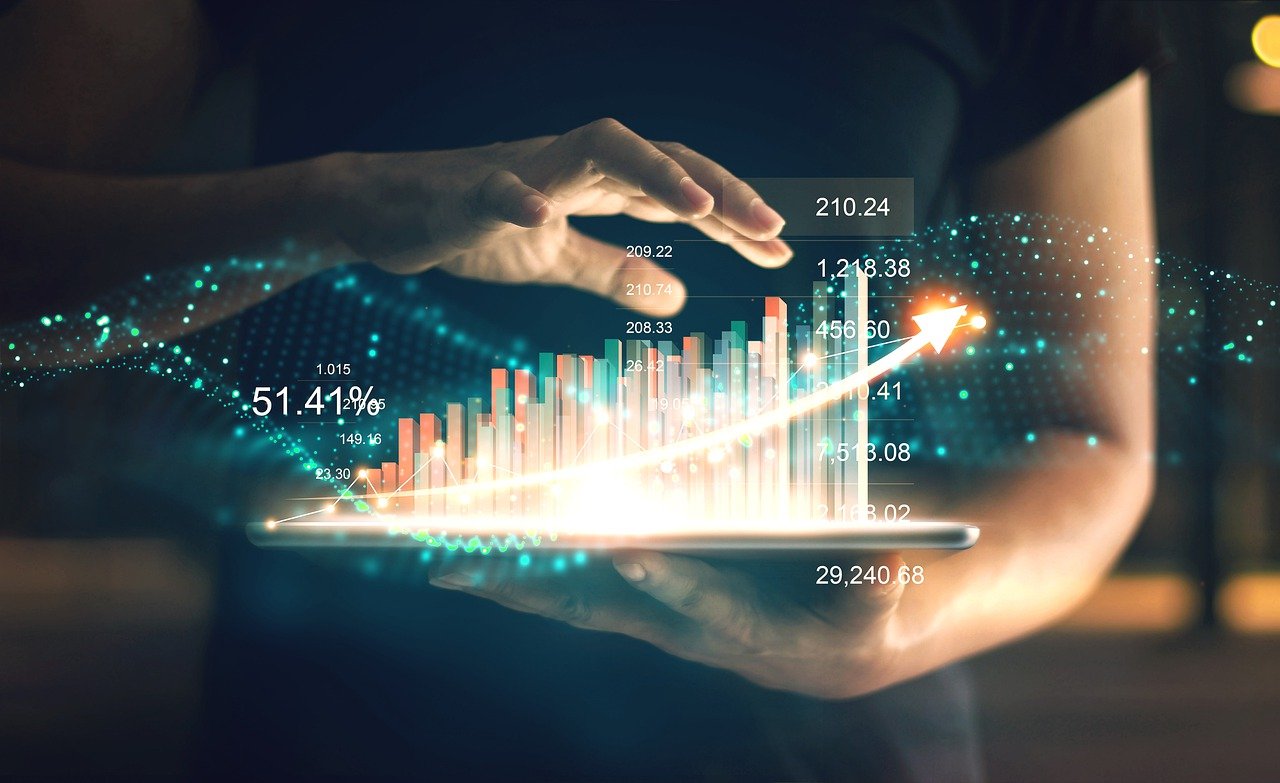
And measurement and reporting are becoming even more sophisticated — giving businesses more information to go on as they make these crucial decisions. More metrics are available, for a fuller view of performance, and there are more ways of evaluating that information once we have it.
This article discusses how those production metrics and methods are evolving.
Measuring Performance in the Past
Traditionally, print shops used some pretty basic measures to see how they were doing. They looked at things like total sales, the number of jobs completed, mistakes, total costs, and how often they delivered on time. These metrics gave a rough idea of how things were going, but they didn't always provide enough detail to pinpoint specific problems or provide actionable data.
But there’s a reason measurement was so rudimentary back then. It’s because collecting that data was also time consuming, completely reliant on manual processes.
Employees would jot down production details like start and finish times, material usage, and any defects on paper forms. Many left these pages in filing cabinets, and a few gathered up and analyzed them to create productivity reports. Some machines had basic sensors to track things like the number of sheets printed, but this data still had to be manually transferred to reporting systems.
Eventually, expensive and challenging Print MIS systems were created that tried to automate the collection of data, offering the ability to create binders filled with three to four inches of computer paper that were printed on dot matrix printers. Unfortunately, the process was time-consuming and prone to errors. It was also high cost, and the data was rarely actionable.
This left companies with a love-hate feeling regarding their Print MIS Systems. They loved the idea of data collection but hated the limited actions they could take.
Thankfully we’ve seen some changes in the years since.
Today’s Metrics and Reporting
Nowadays, the way leading print shops measure productivity has evolved. Modern metrics are much more detailed and actionable, giving a clearer picture of how well things are running. And with actionable data that is specific, relevant, and timely enough to influence decisions and prompt actions, print shops are able to obtain clear insights that can lead to immediate improvements in their manufacturing process.
As an example, let’s imagine that a customer survey showed 60% of customers were unhappy about turnaround time. This is data you can use to take action — maybe changing your staff’s starting time from 9 a.m. to 7 a.m. and introducing a split shift so that some come in later and work until 7 p.m. After putting that into action, a second survey of your customers will find out whether their sentiments have changed. If that change is significant enough, you can continue as is. But if it isn’t, you can choose to make further adjustments to your strategy and continue measuring the results.
This data was actionable and helped you make a change. But the point is that it is not just about gathering numbers — it’s about interpreting those numbers to make informed decisions that enhance efficiency, quality, and customer service.
Key performance indicators (KPIs) like utilization rates, cycle times, and overall equipment effectiveness (OEE) offer a comprehensive view of machine and labor productivity. Metrics like the ratio of good pages printed to bad pages help identify quality issues, and looking at the revenue generated per employee provides insights into labor efficiency and cost management.
Putting Data into Action
The methods for reporting this data have also come a long way.
Barcodes on job tickets and materials are scanned throughout production, automatically capturing data on job status, material usage, and employee activity. This reduces errors and provides real-time tracking.
Integrated print management systems and ERP software automatically gather and analyze data from various sources, giving a real-time view of production metrics. And customer satisfaction surveys and feedback mechanisms add a qualitative measure of print quality and service delivery.
Interactive dashboards display this data in real time, making it easy for managers to spot trends, monitor performance, and make informed decisions quickly.
There are still challenges, of course — including the inability to create dashboards and the lack of integration into other systems such as ERP systems, sales tools, job floor tracking, variable data printing, and mailing. But the shift to modern metrics and advanced reporting methods has dramatically improved the ability to measure and enhance productivity in the printing industry. Advanced data collection and analysis tools offer real-time insights, optimize operations, and ensure higher-quality products are delivered more efficiently.
Conclusion
In the printing industry, tracking production was once done through basic metrics like sales, costs, and on-time deliveries. Data collection was manual and prone to errors, lacking real-time insights.
But modern metrics and reporting methods have evolved to provide more detailed and actionable data, such as utilization rates, cycle times, rework/person and productivity/person, growth per application, estimated versus actual cost, production bottlenecks, and overall equipment effectiveness.
These metrics offer a more comprehensive view of productivity, identifying specific areas for improvement. And that significantly enhances productivity measurement and improvement — leading to optimized operations and higher-quality products.
For modern print businesses, embracing these approaches has become essential for staying competitive in a data-driven and customer-focused market.
The Evolution of Metrics and Reporting in Print Production
Today, modern metrics and reporting are key to staying productive and enhancing performance for print businesses. And measurement and reporting methods have evolved, providing more detailed and actionable data that printers can use to steer their businesses and stay competitive. Explore some of the metrics available to print shops today and learn how measurement has changed over the years — and what that means for today’s print industry.