- Elisha Kasinskas
- |
- May 11, 2016
In this fifth article in the series about the top five challenges facing in-plant print centers, we look at some of the new services in-plants are offering to meet the challenges of growth and relevancy. Expanding workflow features can enable an in-plant to offer new services like VDP and TransPromo.5 Issues-eBook Thumbnail
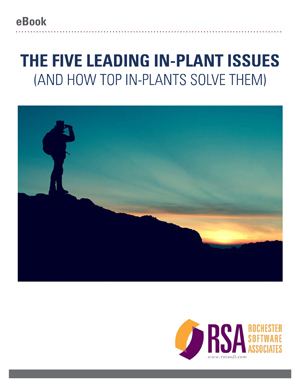
Don't wait for the next articles in the series; download the complete series eBook now, to get valuable insights on the top five issues in-plants are facing.
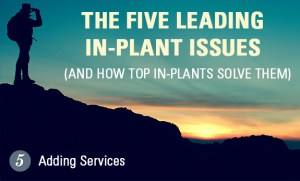
Variable Data Printing (VDP) and Trans Promo
Numerous InfoTrends research notes the VDP potential on a number of fronts: VPD is growing and the adoption of VDP software by in-plants is growing.
Adding VDP offers many benefits to in-plants, ranging from drawing in new business, to reducing cost and touches in the workflow, to increasing flexibility and offering greater brand control. Integrating VDP with Web to print workflow further automates workflow and enables users to order variable content jobs 24 hours per day.
At Sun Life, the in-plant is bringing in new business by adding new VDP products and services for jobs like targeted mail pieces and complex custom booklets – business they would not have been able to secure previously. Applications have included everything from digital photo frames from community service events to customized booklets with over 80 variable data rules and 150 different variables. Plus, VDP services have increased the in-plant's ability to cost-effectively take on smaller jobs such as business cards.
A prominent retirement solutions firm has increased sales for the company and streamlined the order and production process for custom sales presentations for prospective customers. They have created a catalog of "customizable" marketing campaigns and educational materials available in their Web to print platform. On-the-fly edits and proofs are made via the WebCRD Dynamics software. High resolution output is created with no design intervention, and all templates and permutations of variability are pre-approved, so compliance is not an issue. This financial services in-plant has reduced headcount and errors and saved on design resources, while added flexibility to static documents. Most importantly, financial analysts can order and receive their customized marketing material in days rather than weeks.
Government in-plants like the State of Colorado also want to capitalize on personalized messaging, hoping to land new opportunities in Trans-Promo print and mail. Leader Mike Lincoln, Colorado State Printer in the state's Department of Personnel and Administration, Division of Central Services sees Trans-Promo as a largely untapped market in government in-plant printing.
Wide-Format Printing
Wide-format is hot. A 2015 PRIMIR study, "Wide-format Inkjet Printing Trends & Opportunities" projects the wide-format inkjet market to grow to $24.4 billion in 2018.
Key advantages of large-format offerings are the high perceived value and the ability of the offering to increase relevancy. According to a recent InfoTrends update to its study, Wide Format Printing: A Critical Element in the Communications Mix, InfoTrends predicts a compound annual growth rate (CAGR) of 6.7 percent, with growth in all in-plant vertical markets.
However, in-plants face increasing pricing pressure and need to maintain profit margins as commoditization occurs, and find new applications beyond banners, posters and signs. An automated wide format workflow is critical to ensuring wide-format jobs are not a manual process. In RSA's WebCRD software, the system has robust support for users to ticket, receive estimates, and submit orders, and for the print center to produce jobs, and track orders and costs for analysis, billing and chargeback.
Other Services
Professional Services – in-plant Freese and Nichols, Inc., a Fort Worth, Texas-based engineering and architectural firm, offers office furniture ordering using their WebCRD Web to print software. Freese and Nichols is growing and adding offices.
Frees and Nichols Furniture Workflow
The facilities manager needed a way to control, streamline and automate the process offices were using to order furniture. Each office has specific furniture that it can order, controlled by the business rules in the software. Orders are simply placed online as a catalog order. Submitting orders online has improved customer relationships because service has improved (multiple people are automatically notified when an order comes into the print shop), and the firm is tracking and depreciating assets more accurately.
Other services in-plants offer range from scanning, to records management. One of the most progressive in-plants in the United States – Ventura County in California – has converted the business process and document lifecycle into a revenue stream based on eForms, access to data, and advanced marketing services like cross-media. This in-plant has met the challenges facing them head on.
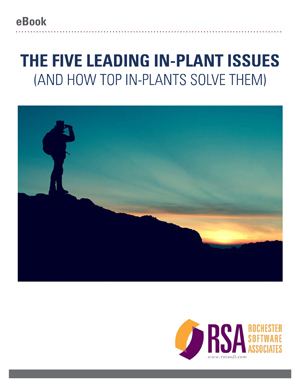
Want to Learn More about the top challenges in-plants face?
Get the free series eBook– with all five articles.
Leave a comment below with your thoughts about how in-plants can be engaged for the future, and be sure to share this 5-part series with your colleagues.