- Elisha Kasinskas
- |
- September 06, 2018
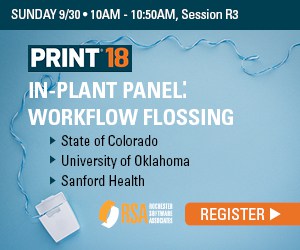
This is the third article introducing each of the three in-plant panelists for the Print 18 "In-Plant Panel: Workflow Flossing" session I'm moderating on September 30th. The panel features in-plant leaders in Healthcare, Government and Higher Education. The in-plant panelists will share their perspectives on workflow and offer their advice for other in-plants. In this post I'm taking a closer look at Sherri Isbell from The University of Oklahoma- the largest University in-plant in the U.S. Isbell describes how workflow is a dynamic, on-going process in her operation, as opposed to being issue or event-driven.
Introducing Sherri Isbell, The University of Oklahoma
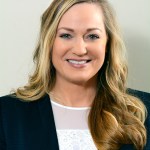
Sherri Isbell is the Associate Director, The University of Oklahoma. Isbell is responsible for Customer Service, Central Mail, Document Services, Offset, Digital and Specialty Printing as well as the Copy Centers and two contract Postal Stations. She is a graduate of the University of Oklahoma and has been a staff member for 28 years. Isbell holds multiple industry certifications, has received recognition for her contributions, and is active in printing industry groups and associations, most notably, the In-plant Printing and Mailing Association (IPMA) where she is President-Elect and a Board member. OU employs 80 staff members, operates with a $16.5M budget and produces 152.8M impressions annually on their offset and digital equipment. This higher education in-plant has won numerous awards and is often a resource for other in-plants for information about equipment and new services.
Ongoing Workflow Work- from "Less than Perfect" to Increased Efficiency Throughout the Shop
One of the questions panelists will address is if working on workflow is event-driven, issue-driven or an ongoing process. When I asked Sherri her thoughts about this, she described how workflow is an ever-evolving process for this top higher education print center. At the University of Oklahoma, workflow changes as their customers change, their demands change and as technology changes. She said, "Every in-plant has a basic process, but we carefully watch and hone ours to fit our needs. During the daily management/production meetings we include a quick audit process to consistently maximize productivity and workflow. We use data collected from 'less than perfect' workflow to better understand gaps and bottlenecks in the process. These information sharing meetings have resulted in a broader knowledge and increased efficiency in all areas of the print shop and even the mail room."
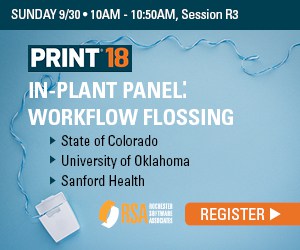
Watch the Full Workflow Flossing Session Here
Join Sherri, me and these top in-plants from around the US to hear how they overcome the hurdles, impediments and challenges of working on workflow and how they "floss"/the process that they use to improve workflow and more.