- Elisha Kasinskas
- |
- August 20, 2020
Tracking Key Performance Indicators (KPIs) is critical for helping commercial printers and in-plant print centers become more productive and profitable. The 2020 North American Production Software Investment Outlook by Keypoint Intelligence/InfoTrends offers useful insights about how the information to create KPIs is collected, how KPIs are used by commercial printers and in-plants, and the KPIs that are most important to those organizations.
Keypoint Intelligence reports that the leading business initiatives for in-plants are reducing production costs and improving efficiency. With staffing levels in flux and budgets more closely scrutinized because of the COVID-19 pandemic, this is an opportune time for in-plants to automate information collection to build KPIs.
Actionable Intelligence is in the KPIs of the Beholder
KPIs are quantifiable measures for monitoring business objectives. Owners and managers often use KPIs for specific projects to determine how well an employee or employees are performing. KPIs can also monitor the costs associated with processing print jobs.
The benefits of using KPIs include cost reduction, the ability to provide management and administration with current data on an operation's efficiency, a reduced need for justification, and increased customer satisfaction.
During these challenging times, access to metrics, understanding those metrics, and repeatedly applying this information to improve overall operations is critical for creating an optimized production environment.
Tracking Operational Performance and How RSA Software Can Help
The Keypoint Intelligence|InfoTrends study identifies the KPIs tracked to monitor operational performance by commercial printers and in-plants.
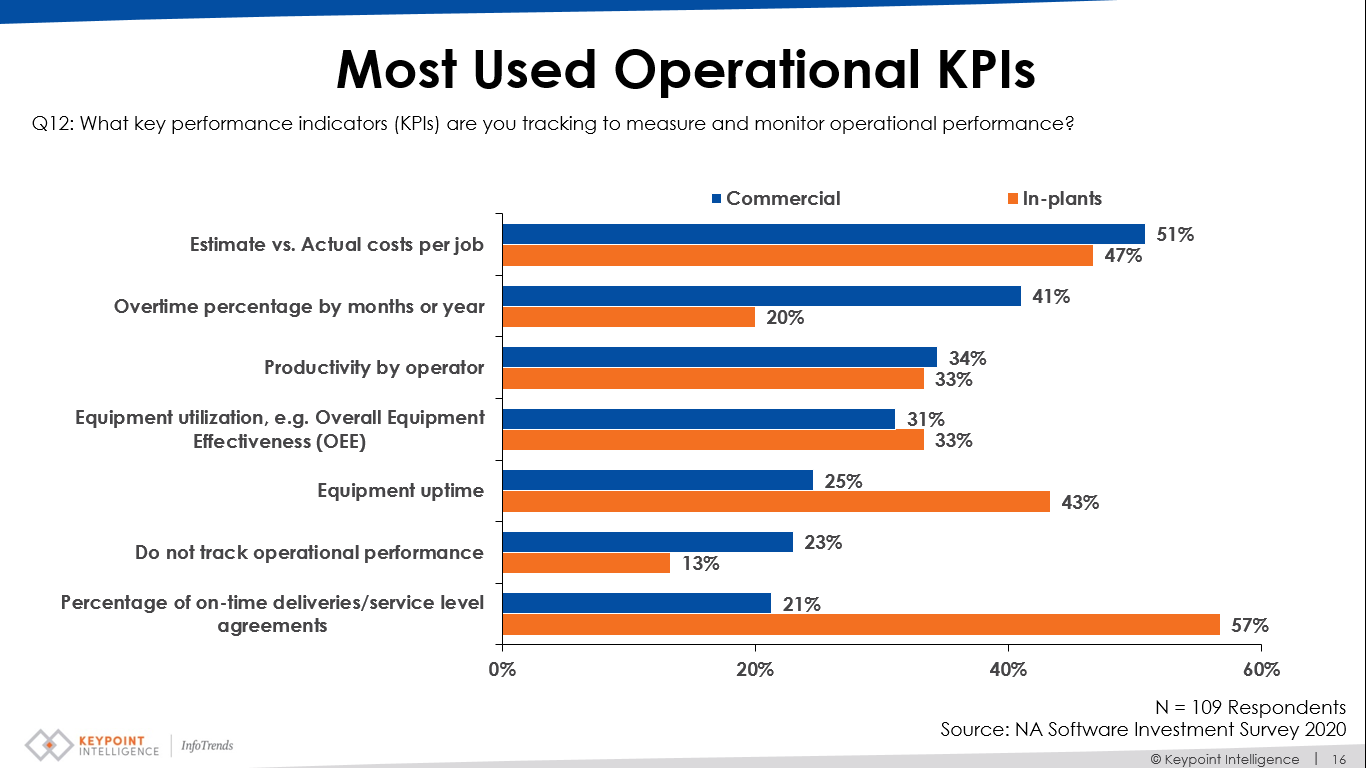
Note the differences between commercial printers and in-plants in the use of KPIs for monitoring on-time deliveries- a key differentiator for an in-house or corporate print center- equipment uptime, and overtime tracking.
The study also found that 23% of commercial printers and 13% of in-plants do not track operational performance. Those are likely tough customers for software resellers to win over, but that doesn't mean one can't try.
Some print production management software, such as WebCRD Web to print from RSA can track this data and display it in a graph or dashboard to pinpoint trends and issues. Examples of KPIs and data analysis that can be produced with operational data include basic volume over time (B/W, color, wide format, revenue, jobs, and orders), operator interactions with the system to process jobs, and orders and revenue by departments and customers. It can also identify the reasons the in-plant is not meeting on-time deliveries. To learn more about WebCRD's dashboards and KPI reporting, download our white paper, "Using your In-plant Data to Improve Efficiency".
Ways to Track Operational KPIs
According the survey, there are various methods used by commercial printers and in-plants for tracking operational KPIs.
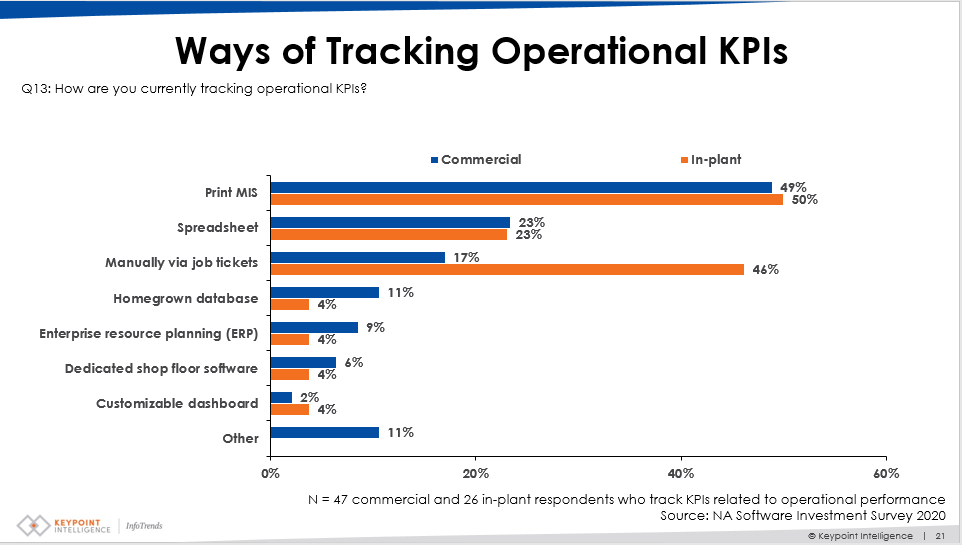
These findings reveal a sizable percentage of in-plants are using manual methods- 46% using job tickets and 23% using spreadsheets– for tracking operational KPIs that can be improved with automation
KPIs are A-OK
If anything can be derived from the study it's that a significant percentage of in-plants are not measuring KPIs and if they are, there may be a better method to do it. Software resellers can work with a production print workflow partner like RSA to identify opportunities and create a talk track about how production management software can monitor an organization's KPIs and improve operations— something that has become increasingly important in the current business climate.
Help Your Customers Improve Their KPI Tracking
Contact your local RSA Business Development Manager to learn how you can successfully help an in-plant improve the tracking of their KPIs with a solution such as WebCRD.