In 2016, we measured a price savings of roughly 50% with our in-plant compared to outside vendors not even counting WebCRD’s added value of easier use, faster turnaround and higher quality output.
Customer Background/Solutions Overview
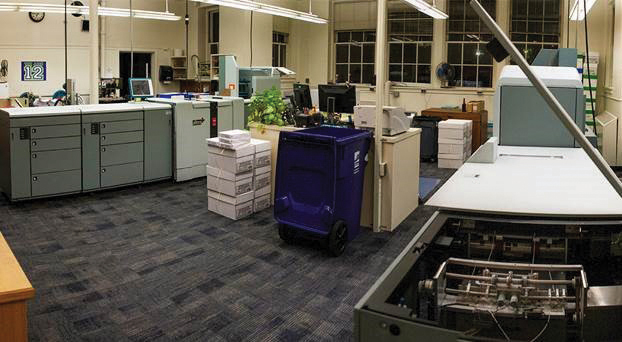
Tacoma Public Schools in Washington State is one of the largest employers in the greater Tacoma area. Their Printing and Graphics department employs three full-time and two half-time staff (4 FTEs) serving 30,000 students and 5,600 staff at 56 schools and learning sites. The print shop creates 15 million impressions each year for faculty, staff and PTA members, producing carbonless forms, business cards, letterhead, envelopes, class materials, report cards, progress reports, and bulk mail.
In the late 1990s through the early 2000s the district used a homegrown print management system. Customers submitted 3-part carbonless forms for every job. The two copies were sent for budget approval that took up to a week, and then one copy was sent to the print shop to be manually entered into the job system. Manual entry took an average of two hours per day. Completed jobs were shipped out with one copy of the job order while another was reviewed to make corrections to pricing. This took another two hours per day. At end of month, the shop generated and printed statements for each school and department sent through district mail. This took another 8 to 12 hours each month.
The print shop sees its role as being an indispensable partner and leader in managing copy and print solutions. They knew they needed to change their inefficient system. In 2012, they began researching Web to print solutions with three clear goals in mind:
- Make teachers' lives easier
- Create a more automated workflow and reduce touch points
- Handle more jobs per month.
The Solution was WebCRD and Continuing Automation
After a brief experiment with a Web to print vendor who went out of business, Tacoma chose WebCRD with the SurePDF™ print driver in June 2011 and went live in March of 2013. The most immediate benefits of leaving hard copy input behind were faster approvals, easier reorders, catalogs and a PDF workflow. Receiving orders from a single source greatly simplified the job onboarding process. “In 2016, we measured a price savings of roughly 50% with our in-plant
compared to outside vendors," says Mike Griswold, Printing and Graphics Lead, Tacoma Public Schools. "That's not even counting WebCRD's added value of easier use, faster turn-around and higher quality output."
We want to help the district close a significant budget shortfall by getting more jobs to our centralized print center. With 35 million annual impressions at our schools, there is a lot of potential for savings.
In 2017, the print shop added more power to their RSA suite with an upgrade to WebCRD and the addition of QDirect, QDirect.SCAN, ReadyPrint Pro and CentralPDF™. While they are ramping up to go live with the additional software, they also recently began using more WebCRD AutoFlow™ rules to move select jobs directly into production.
The current workflow uses WebCRD for job submission, job management (including prepress) and production and reporting. QDirect.SCAN is in pilot for hardcopy job submission from district MFPs. They plan to use QDirect, RSA's output management software to further automate and reduce touches. RSA's prepress software, ReadyPrint Pro is automating frequent prepress tasks such preflighting, document clean up and 2-up and pad printing. They've created workflow templates which automatically impose forms and send them directly to print.
The Significant Results are Measurable in Both Time and Money
"Since we started working with WebCRD, we've gone from 500 to 700 jobs per month without adding staff," says Mike Griswold, Printing and Graphics Lead, Tacoma Public School. "Moving from the old carbonless-based workflow, we've saved 1,100 hours a year, or $44,000 annually in labor. Then there are the improvements for our customers. In the past our minimum turn-around would be 3 days unless orders were hand carried in and picked up. Web submission immediately took a day off turnaround."
Reporting is also enhanced and more robust. Job reporting used to be monthly and took 8 to 12 hours. Now the entire process takes just one hour using WebCRD's charge back reports. "Our RSA rep helped us add files for our reporting that provide a graphical display of cost savings and reduced touchpoints. We use the reports to show improvements to management and track our own growth internally."
The shop continuously adds efficiency to their process. Taking full advantage of WebCRD's rules-based automation engine, AutoFlow, to reduce touchpoints the print shop began adding AutoFlow rules in 2018 and continue to add more in 2019. Using WebCRD's Production and Automation dashboard reports, the shop can see that they have gone from 8 manual touches per job to 4.5 in the 13 months. Reduced touches will save them as much as $50,000 per year (based on $1/touch) or about $94,000 in combined savings.
This is An Important Time to Continue Improving Efficiency
A district budget crisis has caused the district to look more closely at cutting copier program budgets by 10%. "We want to help the district close a significant budget shortfall by getting more jobs to our centralized print center," says Griswold. "With 35 million annual impressions at our schools, there is a lot of potential for savings. We want to make it easier for our customers to submit jobs with QDirect.SCAN for hardcopy job submission right at the MFPs. We will continue to use SurePDF, CentralPDF and Books (our name for the WebCRD Book Assembly module), and with ReadyPrint Pro's Automatica™ we can take advantage of hot folders that will tie it all in with QDirect."
Education Started at the Beginning and Has Never Stopped
Tacoma Public Schools' marketing campaign announcing the launch of WebCRD won an RSA award. They executed the campaign in person, and online through webinars, FAQs and videos that provided step-by-step instructions to users. The shop also put out monthly reports to principals, ads, printed notices included with jobs, and emails.
Today, the print shop staff continues to use all these methods to provide education and raise awareness of their newest capabilities.
© 2019 Rochester Software Associates, Inc. All brands and product names are registered trademarks of their respective companies. 2/2019
Study Quick-Look:
Application Study Industries
Solutions Used by Customer
Challenges
- Manual approval of every job submitted took 3 days
- Too many manual touches to submit and release jobs
- Repetitive manual prepress process for common jobs
Statistics
Students: | 30,000 |
Faculty/ Staff: | 5,600 |
Schools: | 56 |
Impressions: | 15M/yr |
Jobs: | 700 jobs/mo |
Employees: | 4FTEs |
Solutions
- WebCRD™ and multiple modules
- QDirect™
- QDirect.SCAN™
- ReadyPrint™ Pro
Results
- Turnaround accelerated 30%
- $94,000 in labor savings/year
- 40% increase in jobs with existing staff